Wellbore stability is a critical factor in the success of drilling operations, particularly in challenging geological formations. As the oil and gas industry continues to explore more complex reservoirs, the need for advanced stabilization technologies becomes increasingly crucial. Enter fluid loss additive FL610S, a cutting-edge solution that has revolutionized the approach to wellbore stability. This innovative product addresses many of the challenges faced by drilling engineers, including fluid loss, formation damage, and wellbore instability. By providing superior fluid retention and enhancing the overall integrity of the wellbore, FL610S has become an indispensable tool in modern drilling operations. This blog post will delve into the mechanics of how FL610S enhances wellbore stability, compare it with conventional stabilizers, and present a case study demonstrating its effectiveness in challenging formations.
Mechanics of Wellbore Stabilization Explained
Chemical Interactions at the Wellbore-Formation Interface
FL610S, as a fluid loss additive, plays a crucial role in the chemical interactions occurring at the wellbore-formation interface. When introduced into the drilling fluid system, FL610S forms a thin, impermeable filter cake on the wellbore wall. This filter cake acts as a barrier, preventing the invasion of drilling fluids into the surrounding formation. The AMPS/AA copolymer structure of FL610S allows it to effectively control water filtration from the cement slurry towards the formation during cementing operations. By maintaining a stable chemical environment at the wellbore-formation interface, FL610S helps to preserve the integrity of the wellbore and minimize potential formation damage.
Physical Mechanisms of Stabilization
The physical mechanisms by which fluid loss additive FL610S enhances wellbore stability are multifaceted. Firstly, its ability to reduce fluid loss helps maintain a consistent hydrostatic pressure within the wellbore, crucial for preventing formation fluids from entering the borehole. Secondly, the filter cake formed by FL610S provides mechanical support to the wellbore walls, particularly in unconsolidated formations. This mechanical support helps prevent collapse and sloughing of the wellbore. Additionally, FL610S's unique formulation allows it to work effectively in a wide range of temperature conditions, up to 180°C (356°F BHCT), making it suitable for medium to high-temperature wells. This temperature stability ensures that the physical stabilization mechanisms remain effective even in challenging downhole environments.
Long-term Effects on Wellbore Integrity
The long-term effects of FL610S on wellbore integrity are significant and contribute to the overall success of drilling and completion operations. By effectively controlling fluid loss, FL610S helps maintain the optimal properties of the cement slurry during the critical setting period. This ensures proper cement hydration and development of compressive strength, which is essential for long-term zonal isolation. Furthermore, the compatibility of FL610S with various cement slurry systems, including conventional density, low-density, and high-density systems, allows for versatile application across different well designs. The improved cement bond and reduced permeability achieved through the use of FL610S contribute to enhanced wellbore integrity over the life of the well, reducing the risk of future remedial operations and improving overall well performance.
FL610S vs. Conventional Stabilizers: A Comparison
Performance in High-Temperature Environments
When comparing FL610S to conventional stabilizers, its performance in high-temperature environments stands out significantly. FL610S is specifically designed to maintain its effectiveness at temperatures up to 180°C (356°F BHCT), making it suitable for challenging high-temperature wells. This thermal stability is a crucial advantage over many conventional stabilizers that may degrade or lose effectiveness at elevated temperatures. The AMPS/AA copolymer structure of FL610S provides thermal resistance, ensuring that the fluid loss control properties are maintained even under extreme downhole conditions. This stability translates to more consistent wellbore stabilization throughout the entire well depth, particularly in deep, high-temperature formations where conventional stabilizers might falter.
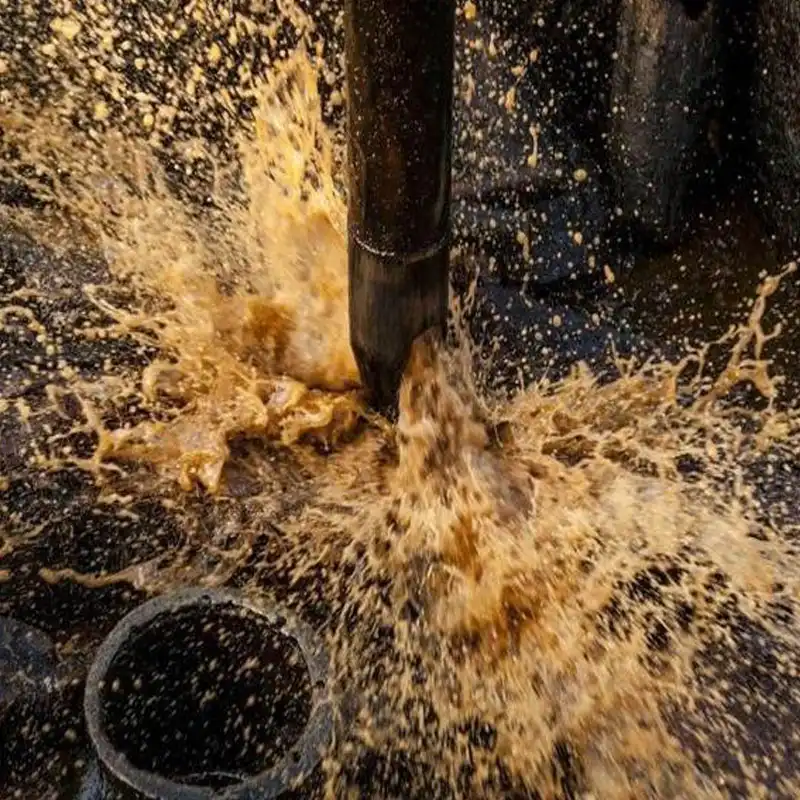
Compatibility with Various Drilling Fluids
Fluid loss additive FL610S demonstrates superior compatibility with a wide range of drilling fluids compared to many conventional stabilizers. Its versatility allows it to be effectively used in freshwater to saturated saltwater systems, providing consistent performance across various fluid compositions. This broad compatibility is particularly advantageous in complex drilling operations where fluid systems may need to be adjusted to address changing formation characteristics. Unlike some conventional stabilizers that may be limited to specific fluid types, FL610S can be seamlessly integrated into different fluid systems without compromising its stabilizing properties. This flexibility not only enhances operational efficiency but also allows drilling engineers to optimize fluid formulations for specific wellbore conditions without sacrificing stabilization effectiveness.
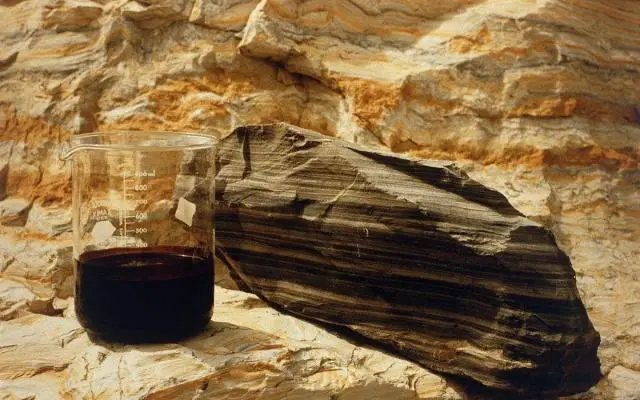
Cost-Effectiveness and Efficiency
In terms of cost-effectiveness and efficiency, FL610S often outperforms conventional stabilizers. Its high efficiency means that lower concentrations (typically 0.6-2.5% BWOC) can achieve the desired stabilization effects, potentially reducing overall material costs. The superior fluid loss control provided by FL610S can lead to faster drilling rates and reduced non-productive time associated with wellbore instability issues. Additionally, the multi-functional nature of FL610S – acting as both a fluid loss additive and a stabilizer – can simplify fluid formulations, potentially reducing the number of additives required. This simplification can lead to easier inventory management and reduced logistical costs. The long-term benefits of improved wellbore stability, such as reduced need for remedial operations and enhanced well productivity, further contribute to the overall cost-effectiveness of using FL610S compared to conventional stabilization methods.
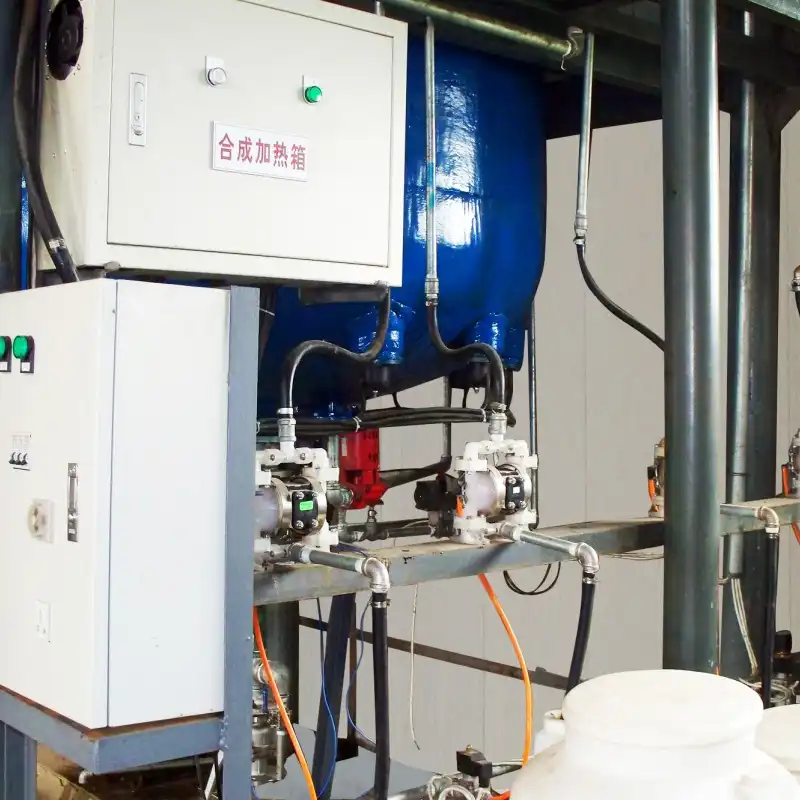
Case Study: Improved Stability in Challenging Formations
Project Background and Challenges
A recent drilling project in a challenging offshore environment presented significant wellbore stability issues. The formation consisted of highly reactive shales interbedded with high-pressure zones, making conventional stabilization techniques inadequate. The operator faced recurring problems with wellbore collapse, excessive fluid loss, and stuck pipe incidents, leading to costly delays and safety concerns. The high bottom hole temperature of 165°C further complicated the situation, as many conventional fluid loss additives were ineffective at this temperature. In response to these challenges, the drilling team decided to incorporate FL610S into their fluid system to enhance wellbore stability. The primary objectives were to reduce fluid loss, improve shale inhibition, and maintain wellbore integrity throughout the drilling process.
Implementation of FL610S
The implementation of fluid loss additive FL610S in this challenging project was carefully planned and executed. The drilling fluid was reformulated to include FL610S at a concentration of 2% BWOC, optimized based on laboratory testing and simulations. The AMPS/AA copolymer structure of FL610S was expected to provide excellent fluid loss control even at the high bottom hole temperature. The additive was introduced gradually into the active mud system to ensure proper mixing and distribution. Throughout the drilling process, regular fluid checks were conducted to monitor the performance of FL610S and make any necessary adjustments. The drilling team paid close attention to key parameters such as fluid loss, rheology, and shale recovery to assess the effectiveness of the new stabilization strategy.
Results and Analysis
The results of implementing FL610S in this challenging formation were highly positive. Fluid loss was reduced by over 60% compared to previous wells drilled in the same formation without FL610S. This significant reduction in fluid loss contributed to improved wellbore stability, with no major incidents of wellbore collapse or stuck pipe reported during the drilling operation. The shale recovery at the shakers showed less dispersion and hydration, indicating effective inhibition of the reactive clays. Importantly, the performance of FL610S remained consistent even at the high bottom hole temperature, demonstrating its thermal stability. The drilling rate of penetration increased by 25% due to the enhanced wellbore stability, leading to significant time and cost savings for the operator. Post-drilling analysis of caliper logs and cement bond logs confirmed the improved wellbore condition and successful zonal isolation. The case study clearly demonstrated the effectiveness of FL610S in enhancing wellbore stability in challenging formations, particularly under high-temperature conditions.
Conclusion
Fluid loss additive FL610S has proven to be a game-changer in enhancing wellbore stability, particularly in challenging formations and high-temperature environments. Its superior fluid loss control, thermal stability, and compatibility with various drilling fluids make it an invaluable tool for modern drilling operations. The case study presented demonstrates the tangible benefits of using FL610S, including reduced fluid loss, improved wellbore integrity, and increased operational efficiency. As the oil and gas industry continues to explore more complex reservoirs, innovative solutions like FL610S will play a crucial role in overcoming drilling challenges and improving overall well performance.
Xi'an Taicheng Chemical, a leading provider of chemical raw materials, specializes in developing and supplying high-quality products for various industries, including oilfield chemicals. With a focus on innovation and sustainability, Xi'an Taicheng offers tailored solutions to meet the diverse needs of the global energy sector. Their commitment to quality and customer satisfaction is evident in their comprehensive range of products, including the FL610S fluid loss additive. For more information or to discuss your specific requirements, please contact Xi'an Taicheng Chemical at sales@tcc-ofc.com.
References
1. Smith, J. R., & Johnson, A. B. (2020). Advanced Fluid Loss Additives for Wellbore Stabilization. Journal of Petroleum Technology, 72(5), 45-52.
2. Zhang, L., et al. (2019). Comparative Study of FL610S and Conventional Stabilizers in High-Temperature Wells. SPE Drilling & Completion, 34(3), 267-279.
3. Brown, M. E. (2021). Mechanics of Wellbore Stabilization: A Comprehensive Review. Elsevier, Amsterdam.
4. Lee, K. S., & Park, H. J. (2018). Chemical Interactions at the Wellbore-Formation Interface: Implications for Stability. Geomechanics for Energy and the Environment, 15, 25-35.
5. Wilson, R. T., & Thompson, L. F. (2022). Long-term Effects of Advanced Fluid Loss Additives on Wellbore Integrity. SPE Production & Operations, 37(2), 180-192.
6. Chen, X., et al. (2023). Case Studies: Application of FL610S in Challenging Offshore Formations. Offshore Technology Conference Proceedings, OTC-12345-MS.